I am having difficulty
- My Lego-like pieces are not sticking to each other, let alone to regular Lego’s.
- Many many of my prints are curling up from the bed.
- My 4? 5? attempts at an iPhone case so far have been incorrectly sized.
- My hexagonal infill is not pretty.
Here is What I have Learned
- When printing really large parts, be aware that ABS filament shrinks. For example, the XY(Z) thing above was 2” while printing (measured with caliper), but as it cooled from 210C down to 27C, it shrunk to 1.98”.
- Enclosures are very important at keeping heat in, which helps a model not-shrink too quickly. Quick shrinking can lead to bends in the structure.
- As the ABS shrinks, in larger parts, the top shrinkage can pull the bottom part off the bed. There are ways around this.. rafts, permiters, skirts, windex cleaning, hairspray sticking, kapton tape, and the heated bed.. As of yet, i haven’t figured out which combination of things will get me a reliable bigger print.
- The Doodle was pretty well configured when i got it. And my tinkering has made it worse.
Of Flow Rates and Stepper Motors, Oh My
As of right now, I’m refusing to learn how to flash/reprogram the eeprom in the doodle. Luckily, the number of steps for the X Y and Z axes are almost dead on. However, the filament stepper is not – its pulling definitely more than 120mm for every 100mm it ought to be pulling.
Luckily, there’s a setting in slic3r that accommodates that – Solidoodle’s config files shipped with a default 0.6 ratio. The result, I thought, was a bit blobby while doing infill. Also, all the documentation said I should have a 0.4mm nozzle, but the configuration was set at 0.5mm; likewise, I was using 1.75mm plastic, but the config said 1.68.
So, i “fixed” them. And slowly, as I scream in 40-minute-delayed frustration, I’m setting them all back.
Luckily, that’s all I’ve had to deal with. Here’s all the things that Solidoodle did RIGHT with the printer, that I have not had to deal with.
- Correctly configured stepper motor sizes
- Correct power levels for the X/Y/Z/etc motors.. potentiometers.. something something.
- Belts are correctly tensioned
- Bed is Level
- Bed is appropriate distance away.
- Nozzle assembly, no jams.
So, GOOD JOB Solidoodle. You did good work here.
Dealing with Spooling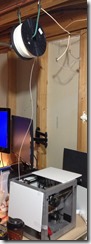
The provided spool holder – bit of a nightmare. It mounts to the back of the printer, but with the XY going all over the place, and with a brand new spool, the slack allows the cable to “fall over” on itself, and it gets wrapped up on the spool handle. My initial solution was to hang a bungee cord from the rafters (I’m in the basement) and run the filament through that – so that gravity is applying a tension for me.
My wife came up with an even better idea: Suspending the Spool from the ceiling with the bungee cord.
Lost My Sense of Direction .. Finding It
I feel like I’ve lost my sense of direction. Where am I trying to go with this printer, and how do I get there?
Part 1: An Education
I’m definitely getting that. Hoo boy. And I’m glad for it. At some time.. next week? next month? I’ll be giving a Lunch and Learn at work on some, or all, of this stuff.. and taking the printer in to work so that other folks can use it, possibly to print their own printers. After what I’ve experienced, if I was to do this again, I’d plunk down the extra money and get an even more pre-built solution – like the Doodle ‘4. I hate messing with stuff. Good luck you guys.
Part 2: Specific Goals
To clear my head up .. which way do I need to / want to go? I need to get this back to being a pleasurable experience, even if I’m failing along the way. (As my wife would say, stop being a booger!)
I Want To [Print] |
Why? |
To Get there, I need to: |
Priority |
Super Serious (not) Lego Minifig Scale model of our current house, possibly with cute little furniture. |
Something inside me.. about representing reality. Its why I do video as well. |
Figure out how to print large prints without warping. |
C5 |
An iPhone case
|
Because then I can print customized cases for my friends and love on them. Q has already requested a Dragonball Z case. |
Get better at exact sizes, large model heat shrinkage, and printing large prints without warping. |
B3 |
Lego-compatible Blocks
|
Because I’d like to incorporate lego nubs on my models, so they are cool. |
Work on wall widths and flow rates, print some calibration pieces that “ought” to stick together, and work on bed lift |
B2 |
Super Action Figure
|
For my nephew Cam, and for my inner 8-y-o. |
Just make time to print a LOT of prints. And precision printing as well. |
C4 |
Pendant thingies |
Because its something my wife can doctor up and make into cool stuff. |
Already there. Just need some design work in Sketchup. Which means I need a design from my wife of what the border should look like. |
Q1 |
Have things figured out enough so that Brandon and Doug can print their printer parts. |
I like being of service and enabling people to investigate cool technologies |
Large print bed lifting and precision. |
B1.5 |
So What is Next? (Given unlimited time)
- Play with their 0.6 ratio default, +/- for More or Less ooze. Figure out where the parts DONT fit, and where they DON’T stay together, and go halfway.
- Double check bed leveling and clearance.
- Print in 0.3mm instead of 0.4mm for a bit.
- Do some Pendants so that I have a sense of accomplishment.
- Print some connector parts, get the connections worked out.
- Retry the Lego’s after connectors are connecting.
- Retry the iPhone Case – with skirt, with raft?, add hairspray, foam core heat shielding, no scaling – measure – apply scaling and retry
- Retry a 2” or 3” print, try to figure out bed lift. (Skirt, raft?, hairspray, heat shielding)
- Take over the world.
Make it so, #1.